Analytical evaluation technology for optimization of structure and molding process of epoxy molded devices
- Akihiro Takizawa
- Yusuke Mori
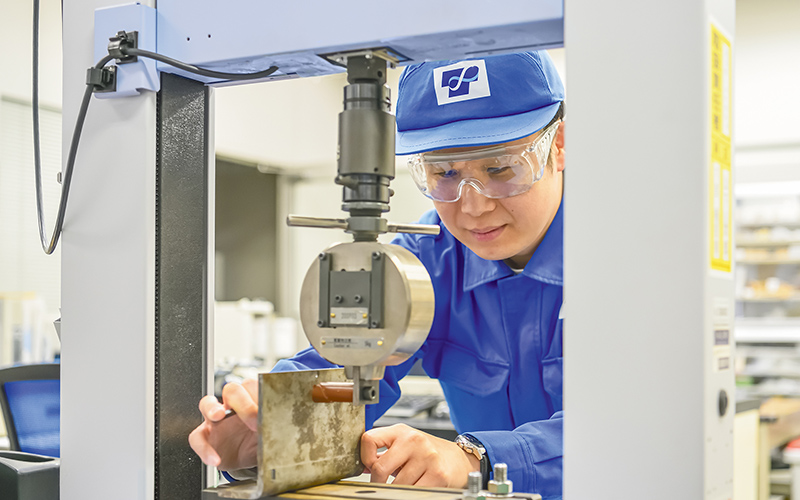
When developing epoxy molded devices, it is necessary to proceed while checking the mechanical strength against thermal stress caused by electromagnetic force and temperature change, but the epoxy resin generates not only stresses caused by these forces but also residual stresses during manufacturing. Because of the difficulty in predicting this residual stress, it was not easy to accurately grasp the state of stress generation and reflect it in the product. This residual stress is complicated because it depends not only on the shape of the product, but also on the forming process, etc., and in these considerations, there were aspects that depended on the experiences of veteran engineers. However, when developing a new product, experience alone may not be enough.
Therefore, for more efficient product development, we are conducting research to visualize the molding process of epoxy molded devices and evaluate the mechanical strength with high accuracy. We will introduce our research that will lead to cost reductions in epoxy molded devices and the development period shortening.
Technology
Correct evaluation of mechanical strength of epoxy molded devices, which was not easy until now.
Epoxy resin is a plastic. Plastics are divided into two types: thermosetting resin and thermoplastic resin, but epoxy resin is thermosetting resin. Thermoplastic resins, which are often used around us, are melted by heat and harden when they cool. Thermosetting resins have the property of causing a chemical reaction and harden when they are heated. When they are once hardened, they do not melt even when they are further heated. Also, they do not melt when cooled. Epoxy resin is characterized not only by heat resistance and flame resistance, but also by excellent electrical insulation and mechanical strength.
We use epoxy resin as a solid insulating material and apply it to molded devices and other insulating media.
Until now, analysis has had the problem of not being able to grasp the mechanical strength after considering various conditions such as residual stress, stress relaxation, and dimensional effects that occur in epoxy-molded devices. In this research, we visualize the hardening reaction and the change in residual stress in the molding process where epoxy resin hardens, and evaluate the mechanical strength to realize appropriate product structural design and mold design.
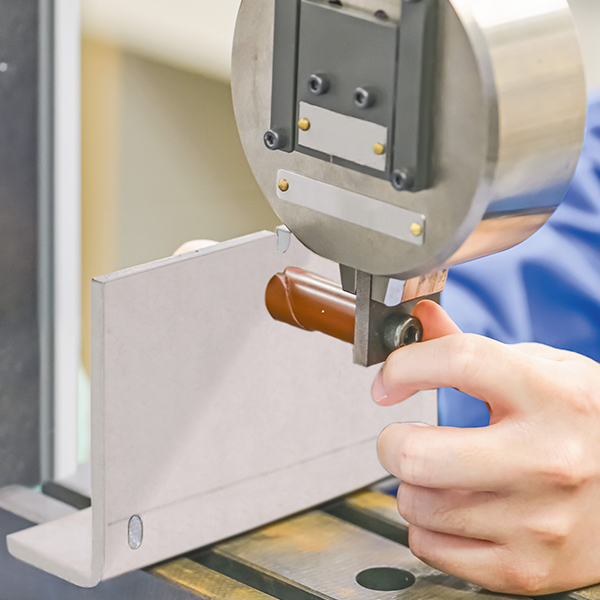
Profile
-
Akihiro TakizawaTechnology Development Division
Research and Development Center
Computer Analysis & High Power Testing Group
Group Manager -
Yusuke MoriTechnology Development Division
Research and Development Center
Computer Analysis & High Power Testing Group
Chief
Visualize the stress applied to equipment and reflect it in product design
Mori:When making epoxy molded devices, epoxy resin is poured into the mold and heated to harden. At that time, it is not possible to see how the resin hardens inside the mold. In that case, you will rely on experience and intuition as to what kind of molding conditions you should proceed with. Through the analysis, we aim to visualize how the resin is hardened in the mold in each molding process, thereby leading to more efficient product development.
Takizawa:Also, when the epoxy resin hardens from liquid to solid, phenomena such as curing shrinkage, stress relaxation, and thermal shrinkage occur during the molding process, and stress remains inside after the molding process. That stress is the residual stress. In order to grasp the residual stress, it is necessary to consider the relationship between the curing reaction of the resin and the volume change. In addition, the viscoelastic properties* and coefficient of linear expansion of resins are temperature-dependent, and we perform analyzes that take these nonlinearities into consideration.
*Viscoelastic properties: Characteristics that combine the properties of an elastic body that deforms instantly when force is applied and the properties of a viscous body that deforms over time
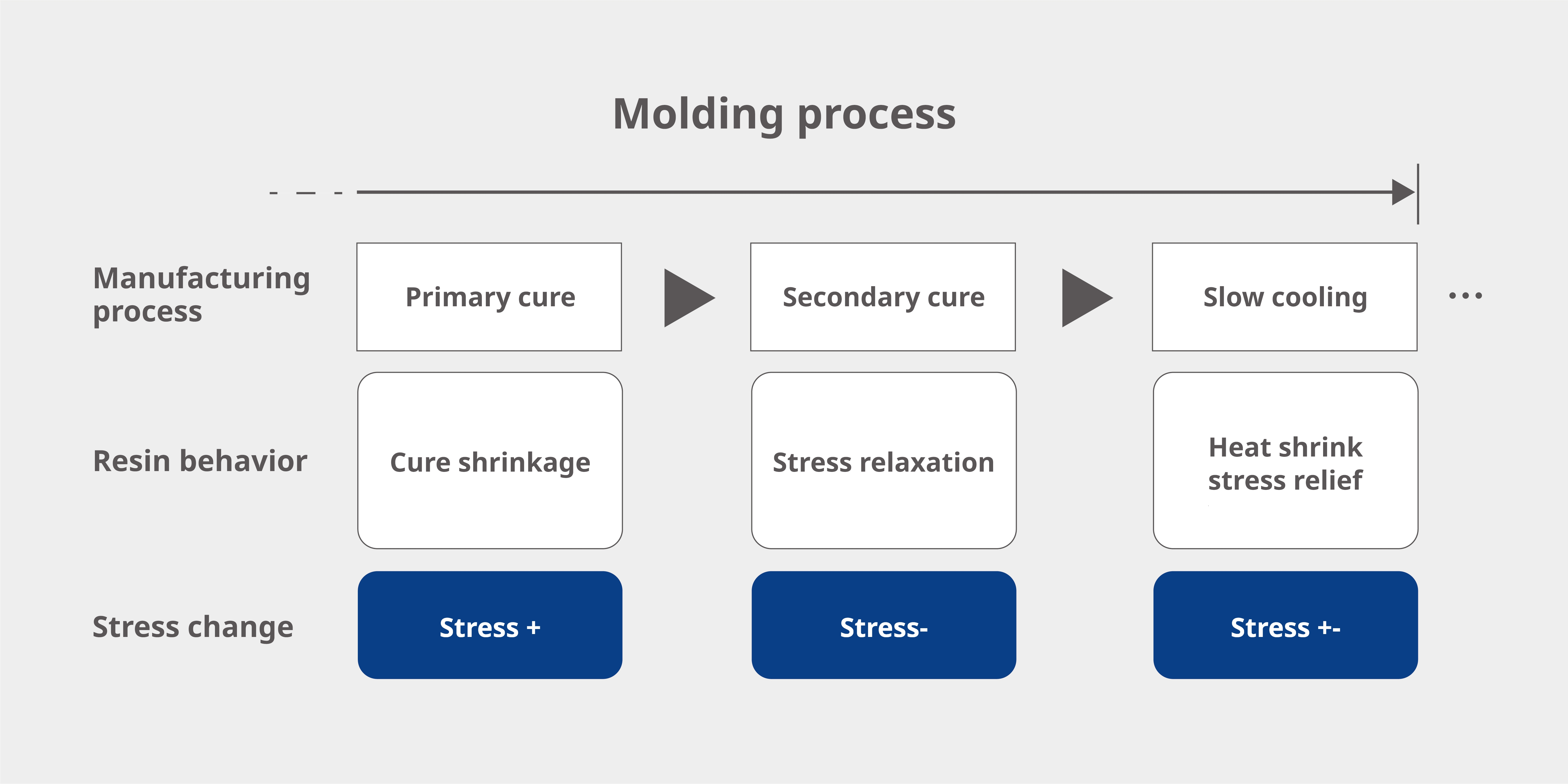
Molding process for epoxy molded devices. There are three stages: primary curing, secondary curing, and slow cooling.
Mori:In addition to the residual stress, the stress distribution when an external force is applied is also analyzed to enable simulations assuming the actual use of the product. Temperature change is assumed to be a stress as an external force expected after the product is released. There are other expected external forces, and we are also considering simulations assuming them.
Takizawa:It is important to accurately evaluate how much external force is applied to cause destruction. In the linear stress analysis that has been generally used so far, there was a gap between the analysis result and the actual breaking load value. It was difficult to obtain an accurate value because the analysis was not performed after considering residual stress and nonlinearity. However, in this research, it is possible to analyze various phenomena that occur in the molding process.
Mori:This research also contributes to cost reduction. In the past, molds were designed based on experience, and sometimes it was necessary to change the shape of the mold. If the analysis shows an appropriate mold from the beginning, there will be no change in the shape of the mold. Changing the mold costs a lot of money, so the cost can be reduced by the results of research. In addition, since remaking the mold can easily take a month or two, it will lead to a shorter development period.
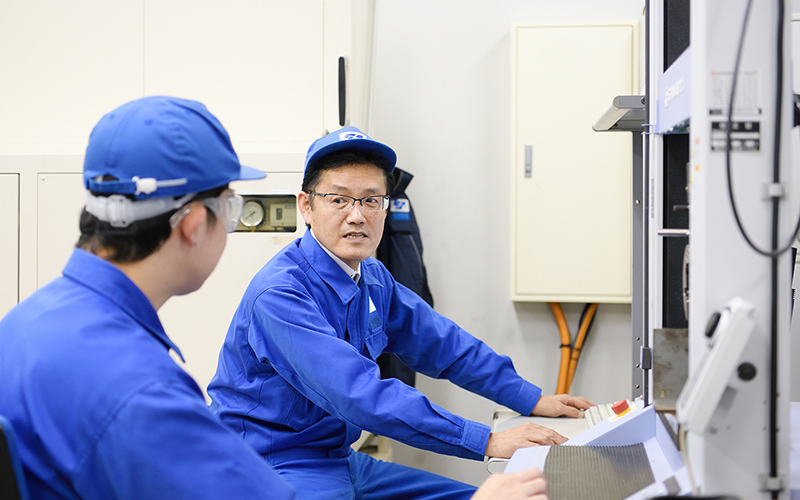
Rewarding of research
Takizawa:I am motivated by the desire to develop new analytical technology so that the people in the related departments can understand the various phenomena that occur in the molding process. Although there were calls within the company for an accurate evaluation of mechanical strength, this was a field that no one had ventured into. Many people consider that this research can be solved by purchasing simulation software. However, the material data used in the simulation is nonlinear and temperature-dependent, and it is necessary to process a large amount of data so that it can be applied to the simulation. This material data processing technology is an inexperienced area and is included in the research content. Sometimes I feel the difficulty as a new challenge. However, when we solve the problem, we feel the joy of acquiring new technologies.
In addition, there are cases where product development was not successful, and when we used simulations to give advice on the product that had been prototyped many times, the problem was immediately resolved. Many new ideas come to me when I am involved in analysis and testing. It is also attractive for research to reflect proposals that are not noticed by designers in products.
Mori: In addition to the analysis, we conduct tests to evaluate the validity of the analysis, compare the analysis and test results, and verify how the analysis method should be improved. I am proceeding through trial and error, so I feel a sense of accomplishment when I use the ideas that come to my mind at that time and get good results.
This research was not only presented in the paper as a technical report, but also presented at the user meeting of the analysis software. It was a great success with many people showing interest and standing in the aisles. The content of our research may seem unspectacular at first glance, but it gave us confidence that we are pioneering advanced fields.
Takizawa:Although this research theme is going to be the final stage, there are many other research themes that need to be verified as analytical technologies. We will continue to develop new analytical technologies that will be useful for product development.
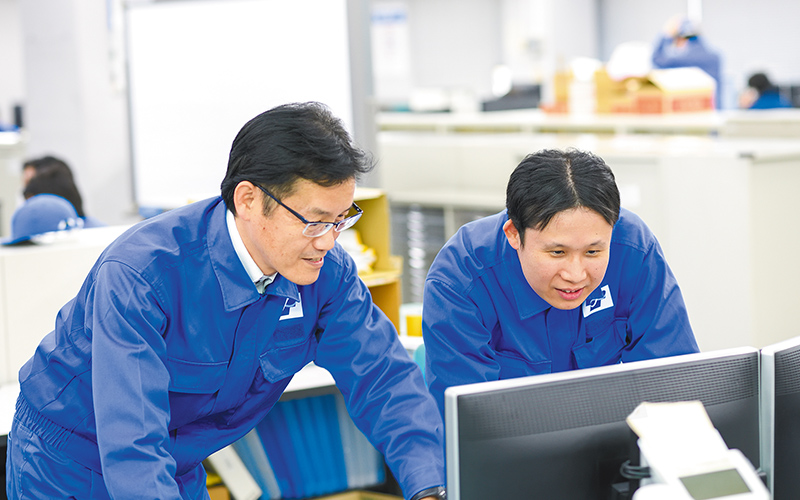
Latest articles
-
interviewProposal for new value via the first steel-tower-type full-color rendering illumination in JapanSince July in 2021, Prifoods Stadium in Hachinohe City, Aomori Prefecture has operated LED illumination equipment capable of the first steel-tower-type full-color light rendering in Japan. Takaoka Toko/Kyoya Denki/CADEC specific construction work consortium accepted an order for this equipment from Hachinohe City, and it was completed after nine months of work.
-
interviewBuilding a microgrid in Ueno Village, Gunma Prefecture, to Achieve Decarbonization and “Zero” Power Outages During a Disaster.The Sixth Strategic Energy Plan, a national policy, states that renewable energy is a main power source, and there is a need to expand the introduction of local power sources, including renewable energy. In recent years, the number of natural disasters in Japan has been on the increase, and a business continuity plan (BCP) is being emphasized for setting forth the methods and measures in advance to minimize the impact of an emergency and to ensure business continuity and a rapid recovery.
-
interviewRecycling technology of transformer oil aiming to achieve carbon neutralityNowadays, the work involved in carbon neutrality and the establishment of a recycling society is essential in business activities. The same trend is observed in the field of transformer oil. The international standard for the quality of transformer oil has been revised; there is now no distinction in quality between new transformer oil and recycled transformer oil (hereinafter “recycled oil”) abroad, which allows them to be treated equivalently.
-
interviewWeCharge: EV charging management system that can be operated in large parking areasEfforts intended to achieve carbon-neutral levels have been made increasingly more often, which requires expansion of the EV charging infrastructure in order to propagate electric vehicles (hereinafter called “EV”).