Monitoring and control systems for IEC61850 compliant digital substations and remote monitoring and control device for distribution substations
- Kazuhiko Narita
- Kazuo Sato
- Haruki Kawamata
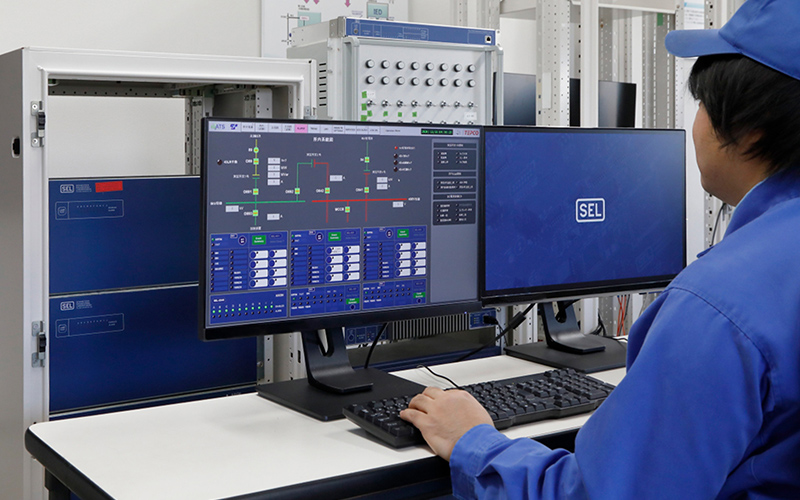
In Japan, we have expanded a variety of equipment to meet the growing demand for electricity as a result of economic development, and have built a highly reliable power supply network. With the recent movement toward electricity liberalization, there is a growing need for higher levels of reliability and efficiency in electric power supply.
The transition to an advanced information society also spurs it. If, for example, a power outage stops a bank or card company's core system, payment for a number of commerce transactions will stop. What will happen if the heating and cooling appliances become unusable in the heat of summer or the cold of winter? There are countless impacts on our lives when electricity stops.
Therefore, in the event of a wide range of power outages, it is demanded more than ever to quickly recover and accurately grasp and disseminate information on where the power outage occurred, what caused the power outage, and how long it will take to restore power. We also have to consider carefully about how to avoid power outages in the first place. What is important is the substation monitoring and control system that underpins power system operation.
To meet this new need for substation monitoring and control systems, TAKAOKA TOKO has developed and marketed a monitoring and control system for digital substations that employs the International Standard IEC61850.
Technology
Promotion of digitization in compliance with IEC61850 which simplifies supervisory and control systems for substations and reduces repair costs.
Monitoring and control systems for substations are installed at substations that perform power transformation and at switchyards that switch power generation and transmission connections. It is used to monitor whether power equipment is operating as expected and to perform operations such as turning on/off power circuit breakers. Other functions include automatic control functions, automatic restoration of failed parts, support for operation and maintenance, and functions that record those movements and can be reviewed later.
Many of the substation equipment installed in the power system expansion period in the late 1980s are becoming increasingly aging for 20 to 30 years, and many of the equipment have reached the renewal period. Under these circumstances, there is a demand for more efficient renewal work, further improvement of reliability, and advanced maintenance and operation. Each substation is planning to promote digitization in order to achieve these goals.
The advantages of digitalization are that the entire equipment can be simplified to reduce costs, and that the monitoring and control system can be separated from the substation equipment and operated remotely. This enables the unified management of multiple substations at one location.
Until now, a large number of metal wires have been laid for each piece of information, from power equipment to devices that collect equipment information, and electrical signals have been used to grasp the conditions and control devices. Digitization in recent years greatly contributes to simplification and cost reductions during updating by replacing a large number of metal lines with the minimum necessary communication lines and exchanging communication data between devices. In addition, it is possible to collect more information.
More than hundreds of digitized substations are built worldwide based on the International Standard IEC61850. It is said that this will become a global standard for the operation and control of electric power systems in the future, and TAKAOKA TOKO is focusing on the construction of a monitoring and control system that employs IEC61850.
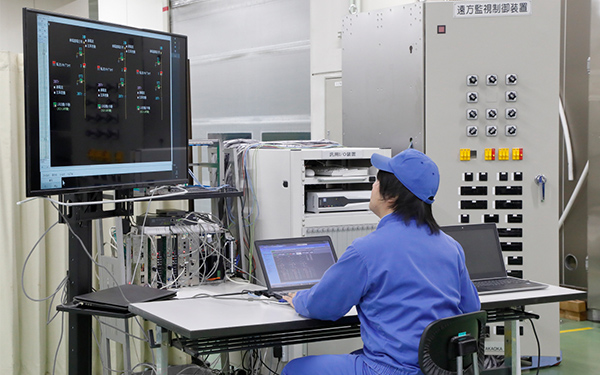
Profile
-
Kazuhiko NaritaPower Equipment & System Business Division
Power Equipment System Manufacturing Department
Protection & Control Equipment Design Group
Deputy section manager -
Kazuo SatoPower Equipment & System Business Division
Power Equipment System Manufacturing Department
Protection & Control Equipment Design Group
Deputy section manager -
Haruki KawamataPower Equipment & System Business Division
Power Equipment System Manufacturing Department
Protection & Control Equipment Design Group
Chief
Expanded versatility by complying with IEC61850
Market competition is also born, and it is an opportunity for better products to be born.
Narita:Conventional systems were created according to the format of a specific vendor, and there was a problem that other vendors could not update the system because they did not understand the mechanism. On the other hand, if it conforms to the International Standard IEC61850, it will be possible for other vendors to support it because the format and mechanism can be shared. In recent years, we have received many inquiries from electric power companies about how to deal with aging substation equipment. While discussing how to proceed, it was decided to apply the International Standard IEC61850. As a result, multiple vendors will develop products based on the same standard, which inevitably leads to market competition and the provision of better products.
Sato:Actually, the performance has improved considerably. Until now, there has been little information that could be sent to the operators due to communication speed issues, and there have been many delays. However, IEC61850 is required to have a fairly high-capacity communication speed in standard formats. In response to it, a large amount of information can be transferred and selected for wide use. In addition, since the vendors themselves have less to think about, IEC61850 conformity reduces the total introduction cost.
Kawamata:For communication, it is possible to use optical fiber or carrier's 4G line, but there are security issues, so currently we do not use wireless communications. All have their own connection method with a high level of security through cables.
Sato:From around September 2017, TEPCO Power Grid and four other manufacturers had meetings, and this project started. Few companies in Japan have know-how about the IEC61850 standard, so I spent every day reading and understanding the standard written in English. The standard has 10 books, some of which exceed 400 pages. However, it is difficult to understand if the books are not systematically read. In fact, I sometimes felt worried while reading them.
Kawamata:We chose to comply with the IEC61850 standard because we wanted versatility. However, we had already developed a device that used IEC61850 in advance, so we decided that TAKAOKA TOKO could do it. We have a technical institute, where we can use the resources obtained there. That was also a deciding factor.
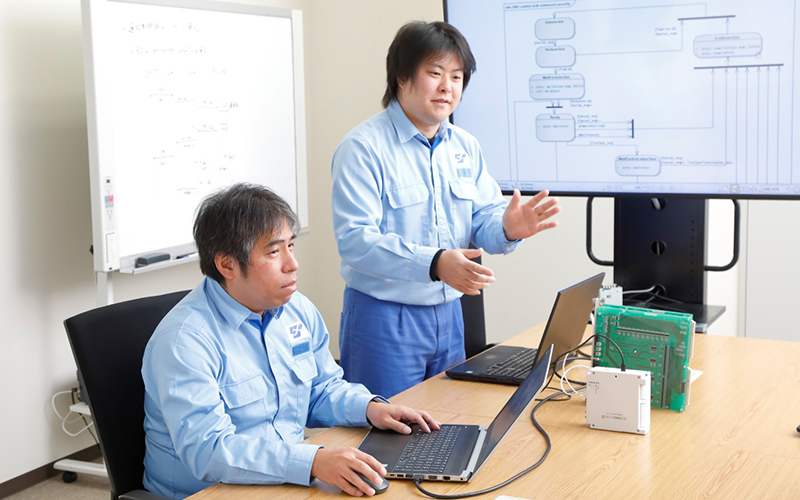
In the future, it will be possible to prevent power outages and other accidents by analyzing big data accumulated through operation.
Narita:The system being verified consists of control, failure display, and measurement display of devices, that is, "SAS (Substation Automation System)" for monitoring and controlling the entire substation, and "BCU (Bay Control Unit)", "PIU (Process Interface Unit)" for transferring power to and from the power plant, and protective relays. Basically, SAS can see all the data, extract only the necessary data from it, and display it on the screen. BCU is gathering data on all the equipment in the substation. For example, it collects information about the state of circuit breakers. This time, it also becomes the final terminal which controls the equipment by receiving the control command from SAS. Protective relays take in current and voltage from the power system, quickly detect failures, etc., in power equipment, and play the role of removing accidents by cutting off the circuit breaker immediately before.
Sato:One of the advantages of digitization is that although, it was necessary to run a long metal cable from power equipment to the I/F (interface) part in the past, digitization makes it possible to control BCU and PIU by connecting them to SAS or TC (teleconverter) via a single cable, if they are placed near the equipment. This significantly reduced the amount of metal cables used, simplifying equipment and reducing repair costs.
Kawamata:We are verifying what other vendors can connect them when it complies with IEC61850 in the future. We plan to conduct this verification through FY2021, including joint verification with each supplier. If this becomes possible, it will be feasible for any vendor to build or update the facility. Today, this is a major challenge. In addition, the data accumulated according to the operation can be shared as big data. By doing so, it will be possible to predict the service life of a facility by analyzing the data to determine how many years the facility will be affected and which parts will fail. Then, for example, preventive maintenance can be expected to predict and avoid the possibility of power outages due to equipment failure.
Narita has studied the field of electronics since his high school days. He joined TAKAOKA TOKO in that direction. He says that he also thinks that he has "assigned to desired department." He says that he enjoys devoting himself to his work every day, and he feels pleased that what he is doing is connected to the future of the company and society.
Sato joined the company after studying power transmission and power generation at university. He says that since joining the company, he has been engaged in many development tasks, and he feels satisfied with constantly learning new things. Nowadays, the keyword IEC61850 is being heard even in our company, and we are starting to be relied on as an experienced member of the department.
Kawamata says that many students joined TAKAOKA TOKO from the same university, he has many seniors and has a high sense of intimacy. He says that when he was a student, he learned electronic control and loved "run according to the program." The way he operates machines shows he is like an eternal machine-loving boy. He says that while doing trial and error, he is enjoying his work.
The three of us are close to each other in the company. When we worry alone, we talk to each other, share information, and encourage each other as we work toward the future of supervisory control technology.
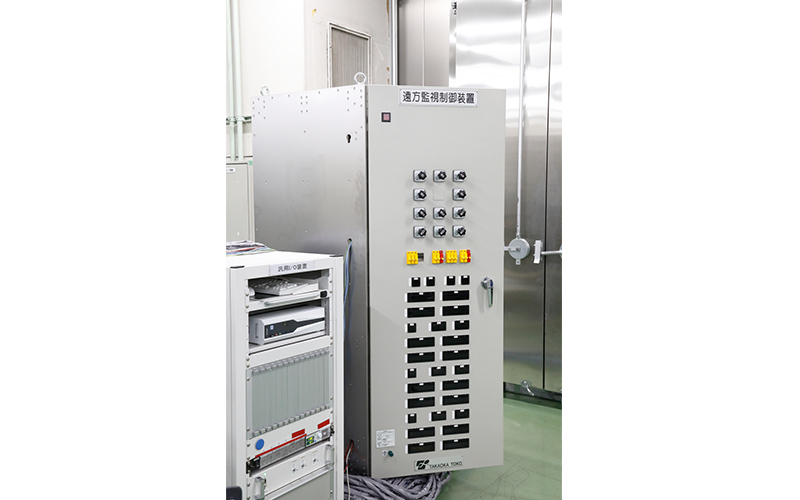
Latest articles
-
interviewThe confocal surface shape measurement system for semiconductor reliabilityIt is no exaggeration to say that semiconductors are used in everything supporting our lives and industry in modern society. Examples include smartphones, home appliances, and industrial products in various fields.
-
interviewImplementation of a Sensor Solution for Substation DigitalizationGlobal energy prices remain at high levels. The presumed cause is the imbalance between energy supply and demand due to recovery in economic activity from the spread of COVID-19, unseasonable weather, disasters, Russia's invasion of Ukraine, and other factors. The soaring energy prices naturally have an impact on the electricity sector, putting not only ordinary households but also electricity suppliers, or electric power companies, in a difficult situation. Power companies are being forced to cut costs to keep power prices down.
-
interviewDevelopment of Techniques for Solar Power Generation Prediction Using AIIn order to promote carbon neutrality, the use of renewable energy that doesn't emit CO2 is expanding.Among renewable energy resources, solar power generation is an important one which will continue to grow in popularity.
-
interviewDevelopment of Medium-Capacity Quick Charger for Electric VehiclesIn anticipation of expansion of EV charging infrastructure in Japan, where the EV shift is accelerating, we worked on the development of the “medium-capacity quick charger (B11)” as a charger that meets the needs for intermediate chargers between normal chargers and quick chargers. This article introduces the features of the product, ingenuity in the development process, and our future vision.