Application of Next-Generation Nanocrystalline Soft Magnetic Materials to Transformer Cores
- Kazuhiro Idei
- Yoichi Matsushita
- Toshiyuki Ozaki
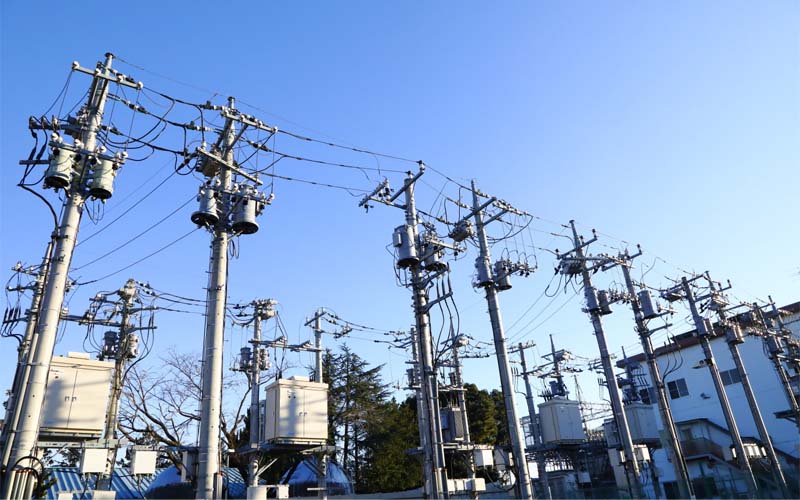
Just hearing the word "transformer" may sound like something unrelated to ordinary people. But just look up at the sky. A utility pole soaring into the blue sky. On top of that utility pole, there is something that supports our lives with all its might. You must have seen it too. A gray object in the shape of a cylinder resembling a bag of rice. That is the "transformer". It is used to convert high-voltage electricity of 6,600V or higher produced at power plants into 200V or 100V for general household use.
Why would you need something like that? Electricity travels from substations to homes through long transmission lines. During that time, some of the electricity is lost as heat due to the electrical resistance of the transmission line. It would be serious if the generated electricity was lost. To minimize this, the voltage is increased and the current is kept low according to the laws of electricity when transmitting power. Then, just before it is sent to the home, it is converted to 200V or 100V with a transformer to reduce loss.
As for the transformer, loss actually occurs when changing the voltage. Since this loss occurs as long as power is being transmitted, minimizing it is an important issue from the viewpoint of both energy conservation and CO2 reduction. To minimize this loss, TAKAOKA TOKO has been improving transformers from various viewpoints, one of which is the use of the next-generation nanocrystalline soft magnetic material NANOMET® in the iron core of transformer.
Technology
Aiming to realize a low-loss transformer that pursues energy conservation through the next-generation nanocrystalline soft magnetic material NANOMET®
Inside a transformer, there is a coil wound around an iron core, and the entire coil is immersed in oil. When an AC current is applied to the input coil, a voltage is generated in the output coil and the voltage changes according to the number of turns of the coil. The role of immersion in insulating oil is to prevent high-voltage electricity from flowing to unintended places and to cool the heat generated during a power transformer.
The material of the iron core greatly affects the loss of electricity when changing the voltage. When a metal, mainly iron, is rapidly cooled from a liquid state at high speed, an amorphous alloy without a crystalline structure can be formed. This is called an "amorphous alloy" and has excellent properties such as magnetic properties, hardness and corrosion resistance. TAKAOKA TOKO has been researching this amorphous alloy for more than 30 years, and has utilized it as a core material for transformers to create low-loss transformers that pursue energy conservation.
Later, from 1998 to 2002, the company participated in a manufacturing research project of transformers using the soft magnetic material of nanocrystal*2 called "NANOPERMTM in a NEDO project*1 of the then Ministry of International Trade and Industry (present the Ministry of Economy, Trade and Industry). Although we were able to make a prototype as a transformer, there was a history that we could not establish the technology for mass production of the material. In response to this, we are currently focusing on "NANOMET®", which is a nanocrystalline soft magnetic material, an alloy developed by Tohoku University that greatly improves the power transport rate, and are working on the development of a compact, high-efficiency transformer.
*1) Project to promote the development of technologies necessary for the realization of a sustainable society
*2) Polycrystalline material with a grain size of several to several tens of nm
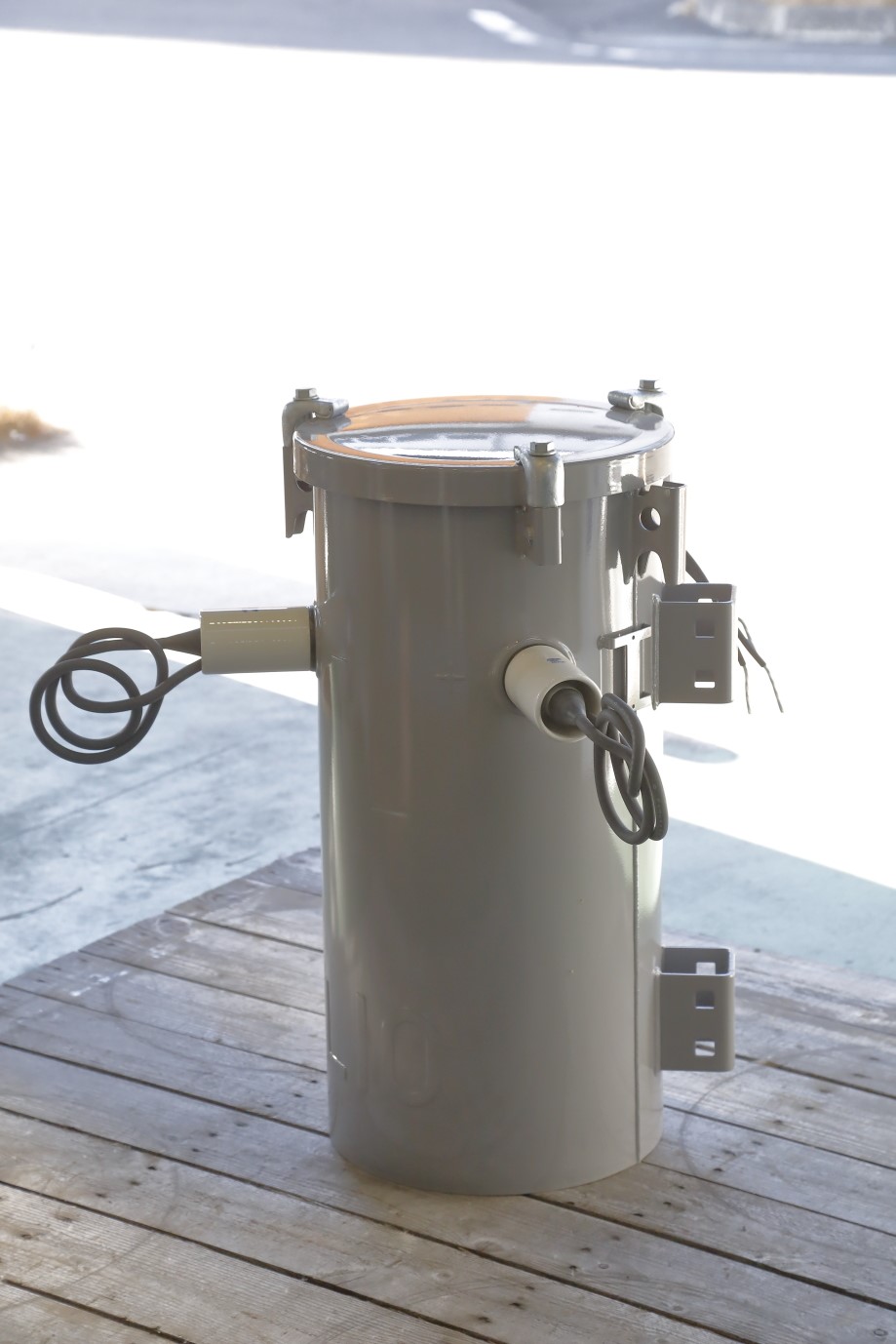
Profile
-
Kazuhiro IdeiTechnology Development Headquarters
Technology Development Division
Materials Technology Group
Section Manager -
Yoichi MatsushitaElectric Equipment Business Division
Distribution Transformer Manufacturing Department
Manufacturing GroupⅠ -
Toshiyuki OzakiPower Equipment Business Headquarters
Small Transformer Manufacturing Department
First Manufacturing Group
Deputy section manager
Challenge to developing environmentally friendly transformers using NANOMET® material, which greatly improves power transport efficiency.
Idei:The development of a transformer using NANOMET® is still in progress, and as of February 2021, the third prototype has been made. NANOMET® has a higher saturation magnetic flux density than the amorphous alloys conventionally used for iron cores, allowing a large amount of magnetic flux to pass through. In short, the higher the saturation magnetic flux density, the more magnetic properties can be maintained even if a large current flows, so the cross-sectional area of the iron core can be made relatively small. This makes the entire transformer more compact. In addition, NANOMET® has another feature that the loss as an iron core is low. Loss is a so-called "iron loss" that is constantly occurring even without load. If this loss is reduced, energy consumption will be reduced, making it possible to create environmentally friendly products.
Matsushita:In addition to iron core materials, technical know-how is also introduced to improve characteristics. We are searching for ways to obtain better characteristics from all angles with less magnetic loss, such as iron core shapes and coil winding methods. Some of the processes are very difficult in actual manufacture, and some can only be done by hand at this stage. However, when it comes to mass production, we cannot handle manual operations. Therefore, there remain major issues related to mass production.
Ozaki:As of now, the magnetic properties targeted by the prototype of the first transformer have been cleared. It is very meaningful to us. However, NANOMET® itself has not reached mass production, and there is still much room for improvement.
Idei:The heat treatment temperature control condition is a key point. At the present, taking steak for example, it could be said to be in a just perfectly grilled state slightly before well done. Roughly speaking, it is an image of slowly grilling over a low heat, taking a whole day or so until the heat is raised and lowered.
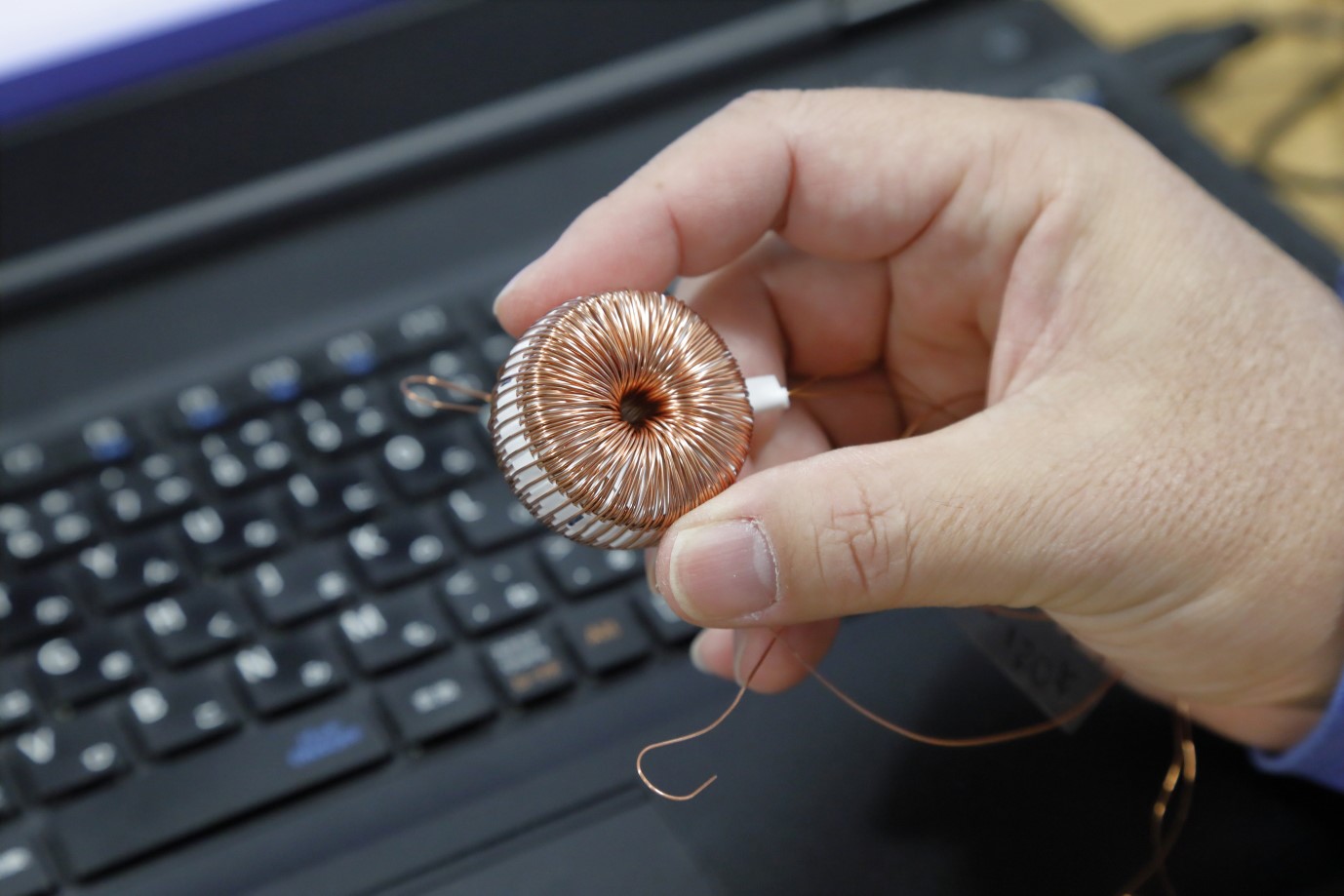

Materials, design and manufacture.
Three experts gather to create next-generation transformers.
Idei:I learned about materials at universities as well, and since joining the company, I have been involved in the research and evaluation of materials for products, and have been developing products.
Matsushita:In the design group, I create design documents for devices, and consider what kind of characteristics we would make, and what other parts should be used to make it. Since this is the first attempt to make a transformer using NANOMET®, we first focus on making it a proper product. In a role we play, once we have a chance to make it into a product, we will then consider the manufacturing cost.
Ozaki:In the manufacturing group, my role is to actually create the products. We design and maintain the tools and devices required for the management of equipment in the plant and the production process. This time, the major challenge is how to switch from the difficult process that is done manually at the test stage to the mass production process. For many years, I have also been involved in the establishment of amorphous transformer manufacturing technology, so I used that know-how to create the necessary jig*3, etc., leading to this measure
*3) A device that fixes a workpiece (processed object) to operate the tool along a guide
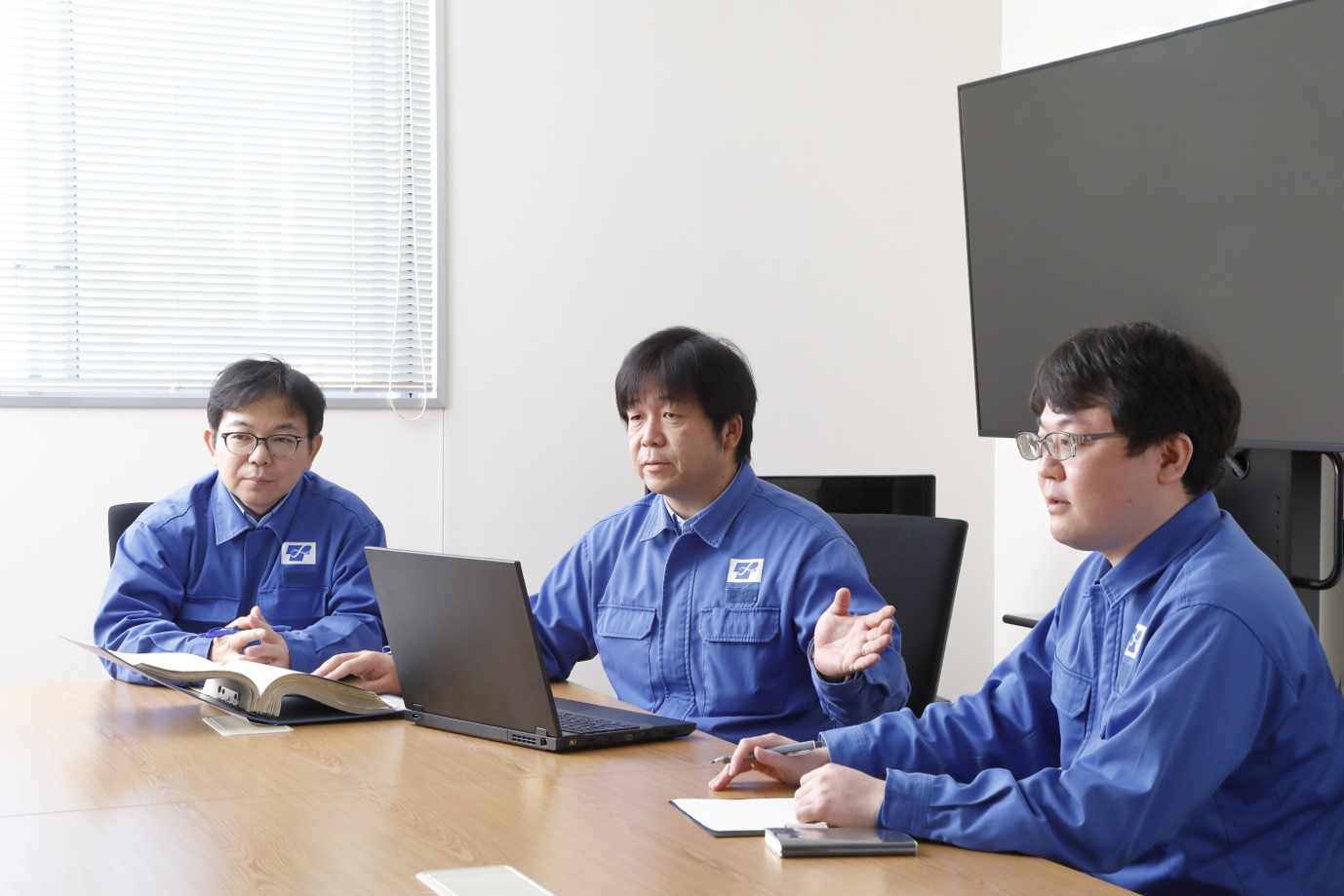
When Idei was in elementary school, he used to disassemble radio-cassette recorders and play with them. He would be unable to repair them and be scolded by his parents. After that, he was unable to understand Ohm's law when studying electricity, and had a trauma to electricity. On the contrary, he joined TAKAOKA TOKO to overcome the trauma.
Matsushita was studying electricity at university, but after joining the company, he learned design from the beginning. He says that he feels happy when he sees something he has designed working properly in the real world and being useful to society.
Ozaki said he saw the inside of a transformer for the first time after joining the company, and was impressed by its unexpected structure. Since then, whatever he is doing, he has become interested in the existence of transformers in the city. He feels every day that it is useful to society.
NANOMET® transformer whose prototype has just been born. Three engineers are now working on the development every day to further improve the characteristics and solve problems for mass production. If the product is developed and put into the world, electric power losses will be reduced, leading to the reduction of CO2 emissions. An international pledge made at the G20 Summit to reduce greenhouse gas emissions to net zero by 2050. As the first step toward fulfilling the commitment to realizing a decarbonized society and a carbon-neutral society, expectations are high for NANOMET® transformers.
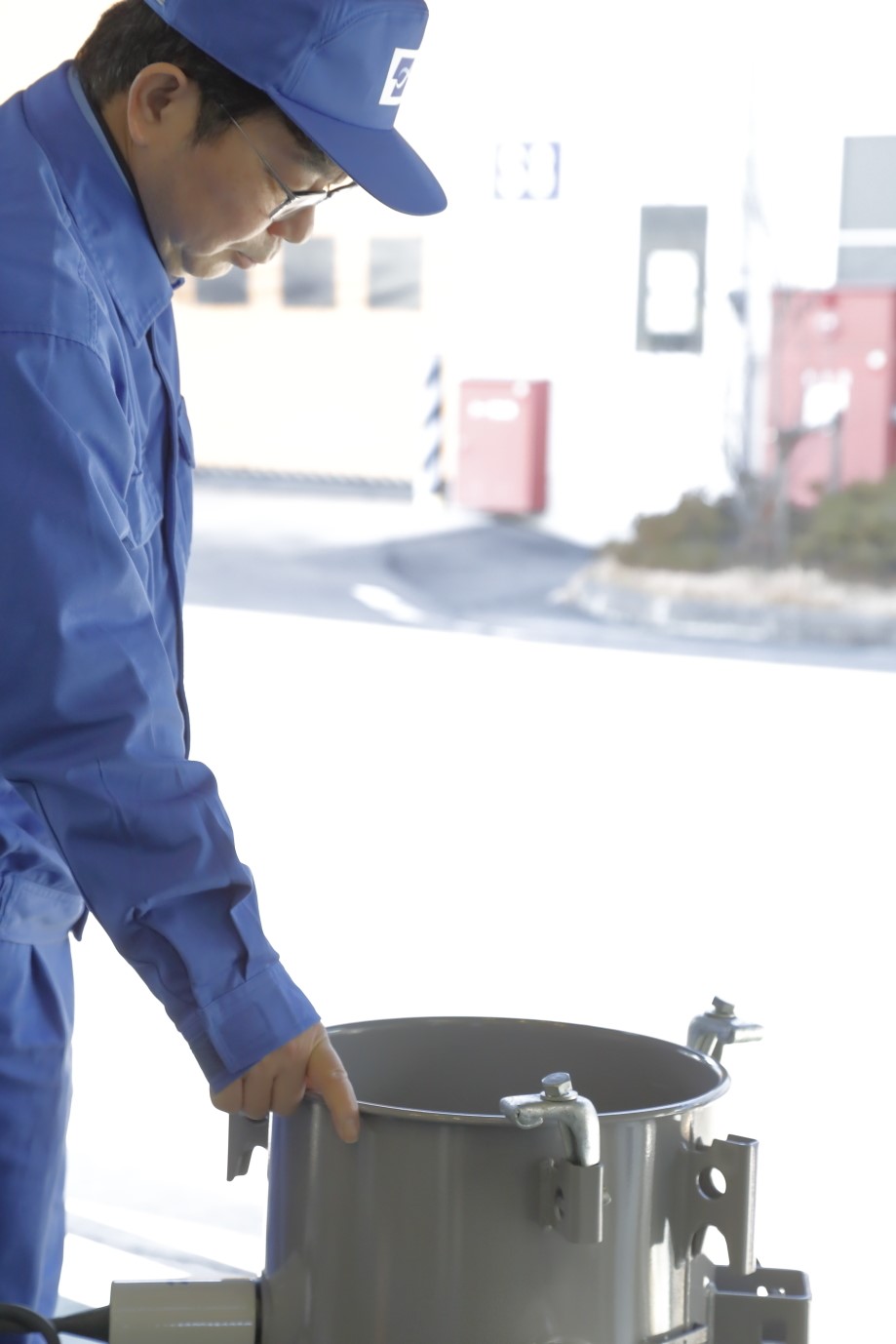
Latest articles
-
interviewThe confocal surface shape measurement system for semiconductor reliabilityIt is no exaggeration to say that semiconductors are used in everything supporting our lives and industry in modern society. Examples include smartphones, home appliances, and industrial products in various fields.
-
interviewImplementation of a Sensor Solution for Substation DigitalizationGlobal energy prices remain at high levels. The presumed cause is the imbalance between energy supply and demand due to recovery in economic activity from the spread of COVID-19, unseasonable weather, disasters, Russia's invasion of Ukraine, and other factors. The soaring energy prices naturally have an impact on the electricity sector, putting not only ordinary households but also electricity suppliers, or electric power companies, in a difficult situation. Power companies are being forced to cut costs to keep power prices down.
-
interviewDevelopment of Techniques for Solar Power Generation Prediction Using AIIn order to promote carbon neutrality, the use of renewable energy that doesn't emit CO2 is expanding.Among renewable energy resources, solar power generation is an important one which will continue to grow in popularity.
-
interviewDevelopment of Medium-Capacity Quick Charger for Electric VehiclesIn anticipation of expansion of EV charging infrastructure in Japan, where the EV shift is accelerating, we worked on the development of the “medium-capacity quick charger (B11)” as a charger that meets the needs for intermediate chargers between normal chargers and quick chargers. This article introduces the features of the product, ingenuity in the development process, and our future vision.