Stress relaxation analysis toward the optimum design of epoxy molded devices
- Ryo Iwai
- Akihiro Takizawa
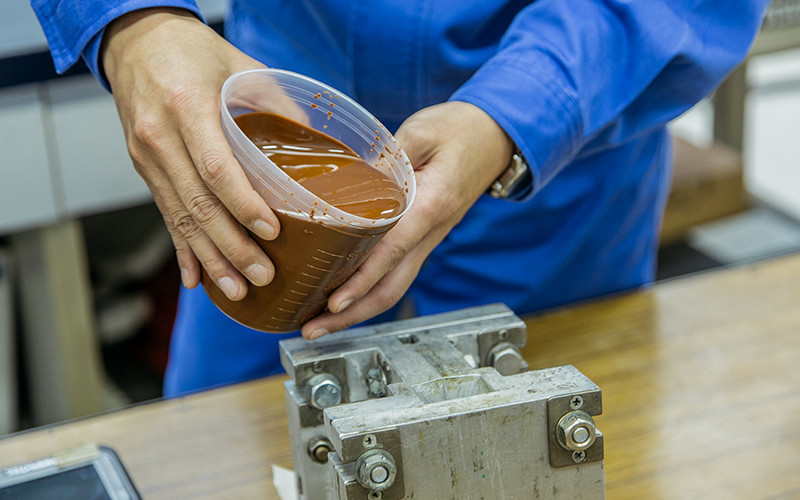
Recently, because of the awareness of disaster prevention and reduction in the environmental load, the need has increased for electric devices considering safety and CO2 emissions. TAKAOKA TOKO has been working to develop electric devices that apply the insulation method using oil and SF6 gas, as well as epoxy resin with superior electric insulation properties and mechanical strength as solid insulation material.
In the future, we must forecast and avoid issues that may occur in the development stage and put products into practical realization as soon as possible in order to respond to social needs more quickly. In the stress relaxation analysis toward the optimum design of epoxy-molded devices, we have conducted research on analysis technologies to set the optimum design and manufacturing conditions in order to enhance the efficiency of molding (manufacturing).
Technology
Realizing product development speed in response to the needs of society and the creation of high-quality products
The resin used for epoxy-molded devices is molded and cured through primary curing, secondary curing, and slow cooling processes.* In order to respond quickly, it is important to determine the optimum molding process conditions for each process to prevent another round of development. The optimum molding process conditions are required to prevent defects, such as voids (tiny hollows) and to reduce residual stress from the cure shrinkage of resin, to prevent the poor appearance of molded surfaces, and to shorten the molding lead-time.
In past research, we developed technologies to analyze resin flow during product manufacturing, resin cure reaction, cure shrinkage, cure strain, and residual stress to obtain optimum molding process conditions. So far, it is possible to analyze the behavior of stress in all processes from primary curing to secondary curing and slow cooling. In the future, we will establish analysis technologies to forecast stress conditions considering the use conditions and to contribute to better product development.
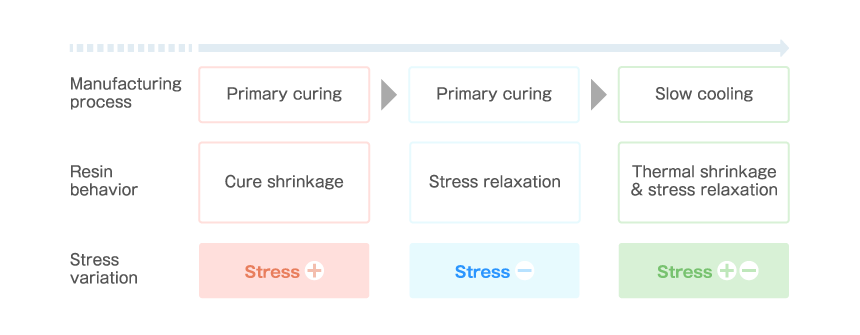
Epoxy molded devices are manufactured through molding processes such as primary curing, secondary curing, and slow cooling processes.
Profile
-
Ryo IwaiResearch & Development Center of Technology Development Division
Manager of Computer Analysis & High Power Testing Group -
Akihiro TakizawaResearch & Development Center of Technology Development Division
Computer Analysis & High Power Testing Group
Establishment of epoxy molded device development environment for safety and the reduction of the environmental load
IwaiAmid the increasing awareness of safety and a reduction in the environmental load, epoxy resin with superior electric insulation property and mechanical strength is widely used as a solid insulation material for electric devices in electric power plants and substations. Compared to the insulation materials of oil and SF6 gas, solid insulation using epoxy molds is largely dependent on the elements of the manufacturer's expertise in resin formulation and manufacturing methods. We intend to provide better products by establishing analysis technologies related to the curing reaction and stress of epoxy molding.
IwaiTAKAOKA TOKO's products are an important component in the supply of electric power. On the other hand, the design and manufacturing conditions for such products differ depending on the sizes, shapes, and materials; consequently, development has been supported by the experience and expertise of skilled engineers.
TakizawaWe are working to change the situation and create an environment to develop general but high-performance products. That is, resin curing analysis technology will be employed in stress relaxation analysis in the optimum design of epoxy-molded devices.
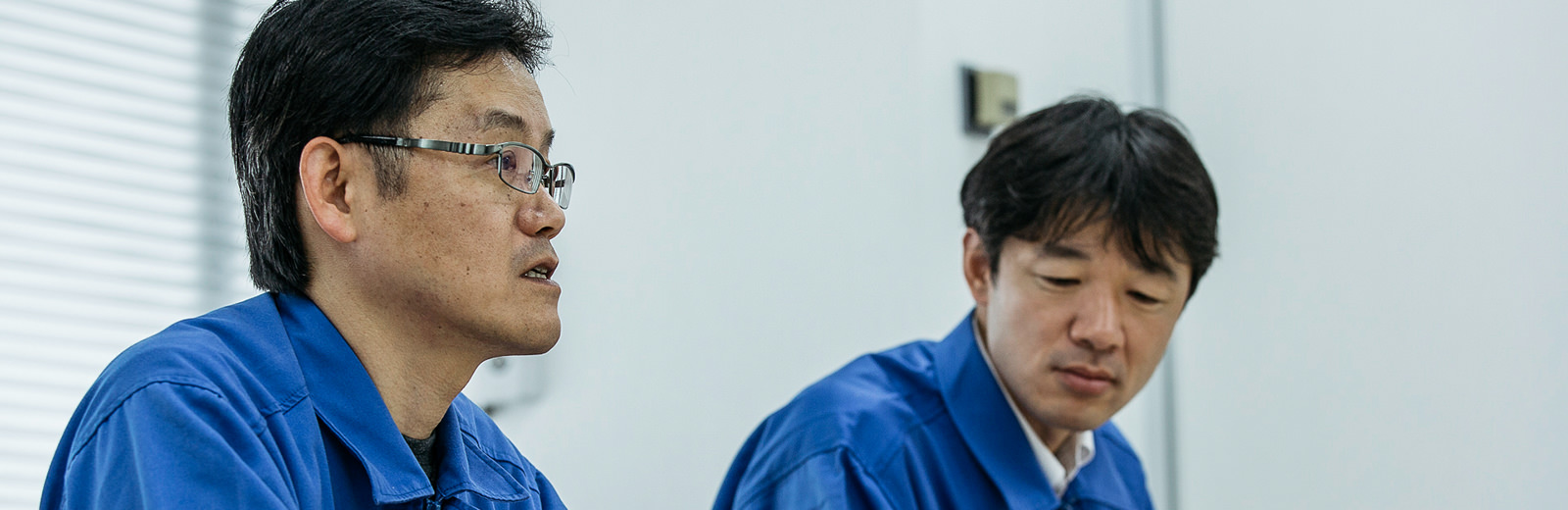
Aiming at the No. 1 technology in the field of epoxy molding with high safety and environmental performance
IwaiTAKAOKA TOKO has been conducting this research with Mr. Takizawa since around 2008. The establishment of the technology for analyzing the stress generated during heating and cooling in the forming process allows us to determine the optimum molding process conditions in the product development stage.
TakizawaRecently, we are sometimes asked to collaborate with other domestic companies, but I remember that we groped in the darkness for what and how to analyze when we started the research. Since there are many kinds of resins with different characteristics of flexibility, weather resistance, and strength, the analysis needs to be made for the multiple molding processes of primary curing, secondary curing, and slow cooling. Therefore, we started by fabricating devices to be analyzed and then found problems under different conditions with different materials and processes to verify the solutions. In the end, we conducted innumerable number of trials.
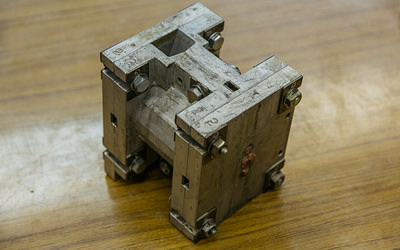
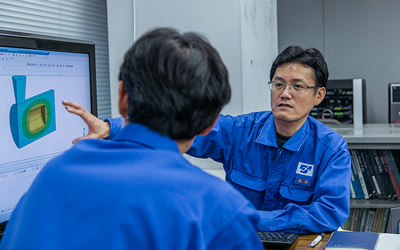
IwaiThere are so many parameters for determining the characteristics of resin that it takes perseverance to collect and verify data each time. Since our research is pioneering, it takes labor and time. Three years ago, I was assigned to my present department, and until that time, I had been designing transformers. Therefore, I have years of experience in this project from a different side such as device structure and performance required for devices.
TakizawaWell, it is a little embarrassing, but we are a good team with broad, deep knowledge, aren't we? Our research has reached the final stage toward practical realization, and I am very glad to see that the products created from our research are helping people.
IwaiI also feel responsibility for and pride in our work supporting Japan's electricity infrastructure. Therefore, I would like to continue to establish the best technologies in the field of epoxy molding with high safety and environmental performance.
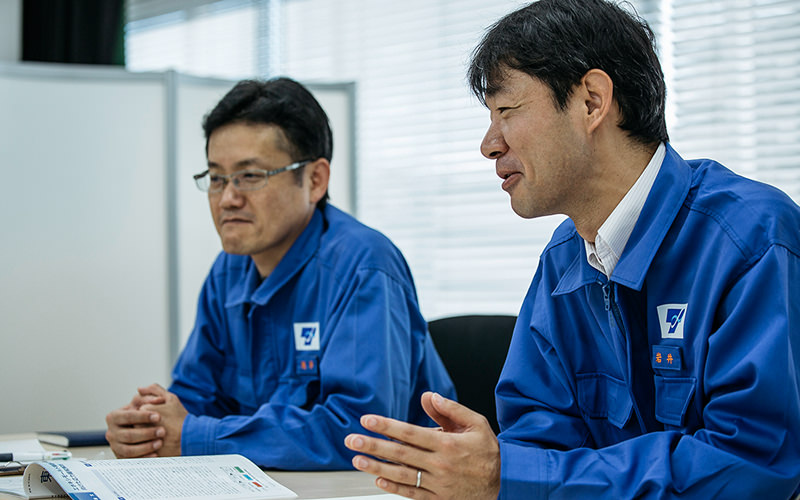
Latest articles
-
interviewThe confocal surface shape measurement system for semiconductor reliabilityIt is no exaggeration to say that semiconductors are used in everything supporting our lives and industry in modern society. Examples include smartphones, home appliances, and industrial products in various fields.
-
interviewImplementation of a Sensor Solution for Substation DigitalizationGlobal energy prices remain at high levels. The presumed cause is the imbalance between energy supply and demand due to recovery in economic activity from the spread of COVID-19, unseasonable weather, disasters, Russia's invasion of Ukraine, and other factors. The soaring energy prices naturally have an impact on the electricity sector, putting not only ordinary households but also electricity suppliers, or electric power companies, in a difficult situation. Power companies are being forced to cut costs to keep power prices down.
-
interviewDevelopment of Techniques for Solar Power Generation Prediction Using AIIn order to promote carbon neutrality, the use of renewable energy that doesn't emit CO2 is expanding.Among renewable energy resources, solar power generation is an important one which will continue to grow in popularity.
-
interviewDevelopment of Medium-Capacity Quick Charger for Electric VehiclesIn anticipation of expansion of EV charging infrastructure in Japan, where the EV shift is accelerating, we worked on the development of the “medium-capacity quick charger (B11)” as a charger that meets the needs for intermediate chargers between normal chargers and quick chargers. This article introduces the features of the product, ingenuity in the development process, and our future vision.